norelem promotes additive manufacturing of lightweight structures
norelem fixes, assembles and moves. The norelem ACADEMY also promotes, in particular, school and student projects such as the FiberFusion project, in which students at ETH Zurich are developing an additive process for 3D printing fibre-reinforced, high-precision polymers. norelem provides the team with significant support in the form of components and know-how.
The targeted promotion of young talent is an integral part of norelem’s corporate philosophy. The norelem ACADEMY is currently supporting the FiberFusion project, consisting of a six-member team from ETH Zurich, which aims to develop continuous 3D printing of fibre-reinforced polymers with high precision. They are working with hybrid bicomponent fibres that enable lightweight construction concepts with high strength. The applications here range from high-precision parts such as watch cases to biomedical products.
The additive manufacturing system consists of a consolidation unit that creates a filament from the bicomponent fibres and an extrusion unit for continuous 3D printing of the filament. norelem supported the construction of the system with pillow block bearings made of stainless steel and grey cast iron, with idler pulleys and keyless locking coupling, angle brackets and gas springs as well as plain bearings and spherical seats.
After defining the system design via rapid prototyping, the focus is now on manufacturing and testing the system. At the end of this phase, a roll-out event is planned, at which the FiberFusion team will present its system at ETH Zurich. norelem is also supporting the team with advice throughout the entire process.
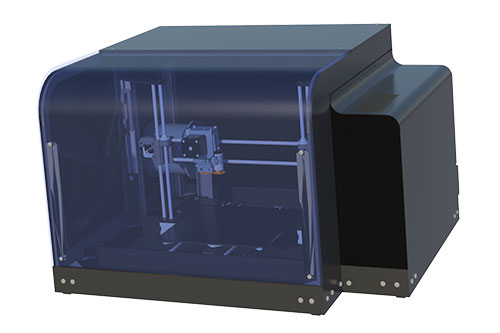
Manufacturing system for 3D printing fibre-reinforced, high-precision polymers.
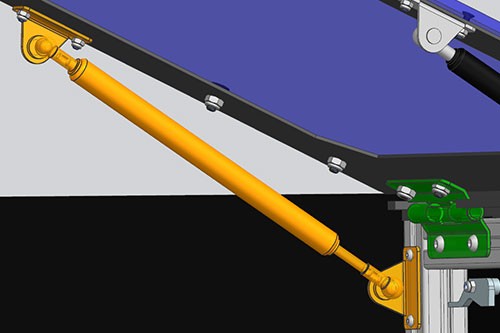
Gas springs from norelem were used in the project to open the printer cover and to attach it to the frame and cover for power transmission.